Hydroxsys and NIG Nutritionals generate clean water from waste products
Clean technology company Hydroxsys has partnered with an Auckland based dairy processor to deliver novel wastewater treatment capability that delivers clean water from the processing of milk and milk products.
NIG Nutritionals has been working with Hydroxsys during the past 12 months to deliver this ‘world first’ technology, and since the start of 2021 has been trialling Hydroxsys equipment at its facility at Paerata, south of Auckland.
The outcome has been the confirmation of the capability of Hydroxsys’ systems in providing a genuine, commercially effective solution to one of the big issues for food processors – management of wastewater from processing operations.
Hydroxsys CEO Mark Hartstone says the company has developed proprietary “world first” filtration technology that challenges current clean in place (CIP) and waste treatment systems not only in dairy, but also wider food and beverage manufacturing and industries like wastewater and mining sectors.
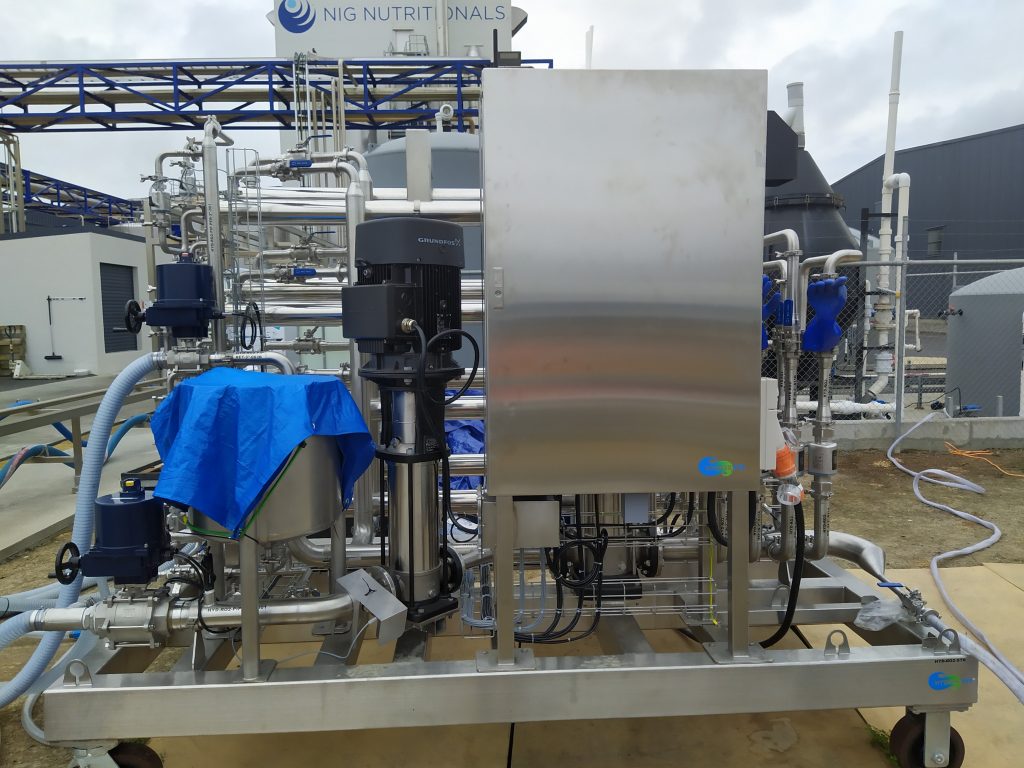
For now, he says, Hydroxsys is focusing on food and beverage (including dairy) manufacturing. Water is a key resource in the manufacturing of all food products and especially milk products.
Hydroxsys comes from the same start-up technology space in Auckland where New Zealand technology champions LanzaTech, Rocket Lab and Mint Innovation found their feet. Now it is following their developmental path by building a commercial sized plant.
The plant at NIG Nutritionals will be complete in about four months and will also be used to demonstrate Hydroxsys’ technology to potential customers.
“Once that plant is operating, it will prove we have scaled our technology from laboratory to mobile demonstration plant and to a commercial operating plant – this one 10 times the capacity of the mobile units we built for field trials,” Mark Hartstone says. “Proving scalability is vital. Delivering this scale within a significantly reduced real-estate footprint is an extra bonus”
Chris Macbeth, CEO of NIG Nutritionals, says liquid milk processing activities generate liquid waste products that need to be treated prior to discharge under consent from Auckland Council and WaterCare.
“NIG Nutritionals values and ethos are built around nurturing our customers with the best in nutritional solutions,” Chris Macbeth says. “This extends to our environment as we believe that what we put into the environment is what we will receive from it in the future.
“With this in mind, we wanted to find new ways of reducing our environmental impact and improving our contribution to environmental sustainability.”
By introducing the Hydroxsys system, NIG Nutritionals substantially improves the quality and cleanliness of its wastewater discharge.
“With the installation of the Hydroxsys process as part of our existing systems, we can effectively reduce our ‘waste’ and return up to 90% of the wastewater volume back to our system as a source of clean water,” Chris Macbeth says.
“Further work will be required to provide assurances that this clean water is able to be recycled back into our manufacturing plants or returned to the environment to replace the water that we take from the aquifer. However, we are very confident, based on the results we have gathered over many months of trials, that we can deliver clean water from our manufacturing processes.”
Hydroxsys’ systems use its proprietary family of polyethylene membrane-based filters, which have been patented internationally.
At NIG Nutritionals solid waste like milk fat, protein and oils are removed from the liquid phase, providing a vastly cleaner waste product. The system doesn’t stop there though and is proven to greatly reduce biological oxygen demand (BOD) and chemical oxygen demand (COD) in the processed waste water, which are key parameters in determining if the water can be released back into the environment.
“We have seen almost 100% effectiveness at removing suspended solids, but what we didn’t expect was the huge reduction in BOD/COD that was also achieved,” Chris Macbeth says.
The solids that are removed also become more concentrated which makes them easier to manage and saves money through reduced treatment systems.
Hartstone and Macbeth agree that this non-toxic solid waste is a future resource and could be used to create new value such as food to worm farms for conversion fertiliser, or for use as a source of safe biomaterial that can be used to generate energy. The waste then becomes a resource.
Of the processed wastewater 95% is reclaimed and has been independently tested by Watercare and shown to be suitable for re-use applications and in some cases to be returned to the environment. Even if the treated water is not discharged to the environment, disposal fees through existing municipal waste treatment plants will be greatly reduced and the demand on those systems reduced, effectively increasing the net capacity of those plants without direct investment costs.
Mark Hartstone says Hydroxsys’ innovative plant is not a huge capital expense and the new technology delivers operational savings. The system has high anti-fouling properties, meaning it can run consistently for days without having to be shut down to clear blockages.
Importantly, the physical footprint of the system is relatively small, and the system itself is modular, meaning it can be purpose built for almost any situation and it does not take up excessive amounts of high value real estate.
“That, combined with our membranes being able to operate at high heat, with greater chemical resistance, and the system being able to capture and recycle those chemicals, means manufacturing plants can save huge amounts of money,” he says, “and we will be releasing more solutions over the next year”.
The waste stream consists of diverse dairy wastewater including washdown, general process cleaning and powder dryer CIP effluent.
- Total Suspended Solids (TSS) was reduced by greater than 99% on input streams
- Fat, oils, and grease (FOG)were reduced by 95% without significant fouling.
- Biological oxygen demand (BOD) was reduced by 65%. The membranes reject about 99.8% of protein in the waste so the residual BOD is mainly composed of residual lactose.
- Chemical oxygen demand was reduced by approximately the same 65%.